Production of rhamnolipids by integrated foam adsorption in a bioreactor system
- PMID: 30043199
- PMCID: PMC6057861
- DOI: 10.1186/s13568-018-0651-y
Production of rhamnolipids by integrated foam adsorption in a bioreactor system
Abstract
Biosurfactants offer environmental as well as health benefits over traditionally used chemical surfactants and heterologous production from engineered microorganisms has been demonstrated, offering containable as well as scalable production of these alternative chemicals. Low product titers and cost intensive downstream processing are the main hurdles for economical biosurfactant production at industrial scales. Increased biosurfactant concentrations are found in the liquid fraction of the foam formed during fermentation of producing microbes. Adsorption of biosurfactants from foam fractions in cultivations may offer a simple concentration and purification method which could enable their cost-effective production. Here, foam adsorption was applied as an in situ method for separation of the rhamnolipid biosurfactants during fermentation of Pseudomonas putida EM383. An integrated process was designed to capture the produced rhamnolipids on hydrophobic adsorbent in packed bed units while minimizing the impact of adsorption on the productivity of the system by recirculating cell-containing collapsed foam flow-through back into the reactor vessel. A stable rhamnolipid production by P. putida EM383 on glucose was performed coupled to this adsorption strategy for 82 h, after which no remaining rhamnolipids were found in the cultivation broth and 15.5 g of rhamnolipids could be eluted from the adsorbent. Rhamnolipid yield from glucose feed was 0.05 g g-1, when up to 2 g L-1 glucose pulse feeding was applied. After solvent evaporation, a product purity of 96% was obtained. The results indicate that the integrated adsorption method can be efficient for simultaneous production and recovery of rhamnolipid biosurfactants from microbial fermentations.
Keywords: Biosurfactant; Foam adsorption; Foam fractionation; Integrated process; Process intensification; Rhamnolipids.
Figures
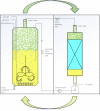
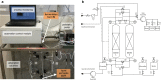
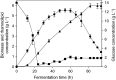

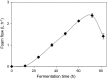
Similar articles
-
Foam adsorption as an ex situ capture step for surfactants produced by fermentation.J Biotechnol. 2017 Sep 20;258:181-189. doi: 10.1016/j.jbiotec.2017.07.015. Epub 2017 Jul 16. J Biotechnol. 2017. PMID: 28723386
-
Integrated foam fractionation for heterologous rhamnolipid production with recombinant Pseudomonas putida in a bioreactor.AMB Express. 2016 Mar;6(1):11. doi: 10.1186/s13568-016-0183-2. Epub 2016 Feb 9. AMB Express. 2016. PMID: 26860613 Free PMC article.
-
Uncoupling Foam Fractionation and Foam Adsorption for Enhanced Biosurfactant Synthesis and Recovery.Microorganisms. 2020 Dec 18;8(12):2029. doi: 10.3390/microorganisms8122029. Microorganisms. 2020. PMID: 33353027 Free PMC article.
-
Recent progress towards industrial rhamnolipids fermentation: Process optimization and foam control.Bioresour Technol. 2020 Feb;298:122394. doi: 10.1016/j.biortech.2019.122394. Epub 2019 Nov 11. Bioresour Technol. 2020. PMID: 31757615 Review.
-
Rhamnolipids--next generation surfactants?J Biotechnol. 2012 Dec 31;162(4):366-80. doi: 10.1016/j.jbiotec.2012.05.022. Epub 2012 Jun 20. J Biotechnol. 2012. PMID: 22728388 Review.
Cited by
-
Foaming of rhamnolipids fermentation: impact factors and fermentation strategies.Microb Cell Fact. 2021 Mar 29;20(1):77. doi: 10.1186/s12934-021-01516-3. Microb Cell Fact. 2021. PMID: 33781264 Free PMC article. Review.
-
Process Development in Biosurfactant Production.Adv Biochem Eng Biotechnol. 2022;181:195-233. doi: 10.1007/10_2021_195. Adv Biochem Eng Biotechnol. 2022. PMID: 35246695 Review.
-
Genetic Cell-Surface Modification for Optimized Foam Fractionation.Front Bioeng Biotechnol. 2020 Oct 29;8:572892. doi: 10.3389/fbioe.2020.572892. eCollection 2020. Front Bioeng Biotechnol. 2020. PMID: 33195133 Free PMC article.
-
Heterologous Rhamnolipid Biosynthesis: Advantages, Challenges, and the Opportunity to Produce Tailor-Made Rhamnolipids.Front Bioeng Biotechnol. 2020 Oct 22;8:594010. doi: 10.3389/fbioe.2020.594010. eCollection 2020. Front Bioeng Biotechnol. 2020. PMID: 33195161 Free PMC article. Review.
-
High-quality physiology of Alcanivorax borkumensis SK2 producing glycolipids enables efficient stirred-tank bioreactor cultivation.Front Bioeng Biotechnol. 2023 Nov 23;11:1325019. doi: 10.3389/fbioe.2023.1325019. eCollection 2023. Front Bioeng Biotechnol. 2023. PMID: 38084272 Free PMC article.
References
-
- Alonso S, Martin PJ. Impact of foaming on surfactin production by Bacillus subtilis: implications on the development of integrated in situ foam fractionation removal systems. Biochem Eng J. 2016;110:125–133. doi: 10.1016/j.bej.2016.02.006. - DOI
-
- Chandra R, editor. Advances in biodegradation and bioremediation of industrial waste. Boca Raton: CRC Press; 2015.
LinkOut - more resources
Full Text Sources
Other Literature Sources