Uncoupling Foam Fractionation and Foam Adsorption for Enhanced Biosurfactant Synthesis and Recovery
- PMID: 33353027
- PMCID: PMC7766737
- DOI: 10.3390/microorganisms8122029
Uncoupling Foam Fractionation and Foam Adsorption for Enhanced Biosurfactant Synthesis and Recovery
Abstract
The production of biosurfactants is often hampered by excessive foaming in the bioreactor, impacting system scale-up and downstream processing. Foam fractionation was proposed to tackle this challenge by combining in situ product removal with a pre-purification step. In previous studies, foam fractionation was coupled to bioreactor operation, hence it was operated at suboptimal parameters. Here, we use an external fractionation column to decouple biosurfactant production from foam fractionation, enabling continuous surfactant separation, which is especially suited for system scale-up. As a subsequent product recovery step, continuous foam adsorption was integrated into the process. The configuration is evaluated for rhamnolipid (RL) or 3-(3-hydroxyalkanoyloxy)alkanoic acid (HAA, i.e., RL precursor) production by recombinant non-pathogenic Pseudomonas putida KT2440. Surfactant concentrations of 7.5 gRL/L and 2.0 gHAA/L were obtained in the fractionated foam. 4.7 g RLs and 2.8 g HAAs could be separated in the 2-stage recovery process within 36 h from a 2 L culture volume. With a culture volume scale-up to 9 L, 16 g RLs were adsorbed, and the space-time yield (STY) increased by 31% to 0.21 gRL/L·h. We demonstrate a well-performing process design for biosurfactant production and recovery as a contribution to a vital bioeconomy.
Keywords: 3-(3-hydroxyalkanoyloxy)alkanoic acid (HAA); biosurfactant; foam adsorption; foam fractionation; integrated product recovery; metabolic engineering; rhamnolipid; scale-up.
Conflict of interest statement
The authors declare no conflict of interest. The funders had no role in the design of the study; in the collection, analyses, or interpretation of data; in the writing of the manuscript, or in the decision to publish the results.
Figures
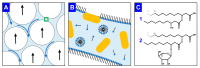
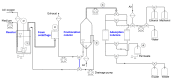
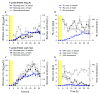
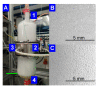
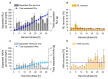
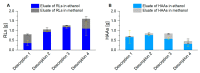
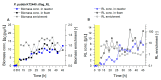
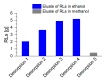
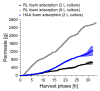
Similar articles
-
Genetic Cell-Surface Modification for Optimized Foam Fractionation.Front Bioeng Biotechnol. 2020 Oct 29;8:572892. doi: 10.3389/fbioe.2020.572892. eCollection 2020. Front Bioeng Biotechnol. 2020. PMID: 33195133 Free PMC article.
-
Integrated foam fractionation for heterologous rhamnolipid production with recombinant Pseudomonas putida in a bioreactor.AMB Express. 2016 Mar;6(1):11. doi: 10.1186/s13568-016-0183-2. Epub 2016 Feb 9. AMB Express. 2016. PMID: 26860613 Free PMC article.
-
Production of rhamnolipids by integrated foam adsorption in a bioreactor system.AMB Express. 2018 Jul 24;8(1):122. doi: 10.1186/s13568-018-0651-y. AMB Express. 2018. PMID: 30043199 Free PMC article.
-
In situ downstream strategies for cost-effective bio/surfactant recovery.Biotechnol Appl Biochem. 2018 Jul;65(4):523-532. doi: 10.1002/bab.1641. Epub 2018 Feb 21. Biotechnol Appl Biochem. 2018. PMID: 29297935 Review.
-
Foam fractionation methods in aerobic fermentation processes.Biotechnol Bioeng. 2022 Jul;119(7):1697-1711. doi: 10.1002/bit.28102. Epub 2022 Apr 22. Biotechnol Bioeng. 2022. PMID: 35394649 Review.
Cited by
-
Achieving "Non-Foaming" Rhamnolipid Production and Productivity Rebounds of Pseudomonas aeruginosa under Weakly Acidic Fermentation.Microorganisms. 2022 May 25;10(6):1091. doi: 10.3390/microorganisms10061091. Microorganisms. 2022. PMID: 35744608 Free PMC article.
-
High-quality physiology of Alcanivorax borkumensis SK2 producing glycolipids enables efficient stirred-tank bioreactor cultivation.Front Bioeng Biotechnol. 2023 Nov 23;11:1325019. doi: 10.3389/fbioe.2023.1325019. eCollection 2023. Front Bioeng Biotechnol. 2023. PMID: 38084272 Free PMC article.
-
Evaluation of an external foam column for in situ product removal in aerated surfactin production processes.Front Bioeng Biotechnol. 2023 Nov 6;11:1264787. doi: 10.3389/fbioe.2023.1264787. eCollection 2023. Front Bioeng Biotechnol. 2023. PMID: 38026897 Free PMC article.
-
Removal of heavy oil from contaminated surfaces with a detergent formulation containing biosurfactants produced by Pseudomonas spp.PeerJ. 2021 Nov 25;9:e12518. doi: 10.7717/peerj.12518. eCollection 2021. PeerJ. 2021. PMID: 34900433 Free PMC article.
References
-
- Kosaric N., Vardar-Sukan F. Biosurfactants. CRC Press Taylor & Francis Group; Boca Raton, FL, USA: 2015.
Grants and funding
LinkOut - more resources
Full Text Sources
Research Materials