Evaluation of an external foam column for in situ product removal in aerated surfactin production processes
- PMID: 38026897
- PMCID: PMC10657896
- DOI: 10.3389/fbioe.2023.1264787
Evaluation of an external foam column for in situ product removal in aerated surfactin production processes
Abstract
In Bacillus fermentation processes, severe foam formation may occur in aerated bioreactor systems caused by surface-active lipopeptides. Although they represent interesting compounds for industrial biotechnology, their property of foaming excessively during aeration may pose challenges for bioproduction. One option to turn this obstacle into an advantage is to apply foam fractionation and thus realize in situ product removal as an initial downstream step. Here we present and evaluate a method for integrated foam fractionation. A special feature of this setup is the external foam column that operates separately in terms of, e.g., aeration rates from the bioreactor system and allows recycling of cells and media. This provides additional control points in contrast to an internal foam column or a foam trap. To demonstrate the applicability of this method, the foam column was exemplarily operated during an aerated batch process using the surfactin-producing Bacillus subtilis strain JABs24. It was also investigated how the presence of lipopeptides and bacterial cells affected functionality. As expected, the major foam formation resulted in fermentation difficulties during aerated processes, partially resulting in reactor overflow. However, an overall robust performance of the foam fractionation could be demonstrated. A maximum surfactin concentration of 7.7 g/L in the foamate and enrichments of up to 4 were achieved. It was further observed that high lipopeptide enrichments were associated with low sampling flow rates of the foamate. This relation could be influenced by changing the operating parameters of the foam column. With the methodology presented here, an enrichment of biosurfactants with simultaneous retention of the production cells was possible. Since both process aeration and foam fractionation can be individually controlled and designed, this method offers the prospect of being transferred beyond aerated batch processes.
Keywords: Bacillus; aerated fermentation processes; downstream processing; foam fractionation; in-situ product removal; surfactin.
Copyright © 2023 Treinen, Claassen, Hoffmann, Lilge, Henkel and Hausmann.
Conflict of interest statement
The authors declare that the research was conducted in the absence of any commercial or financial relationships that could be construed as a potential conflict of interest. The author(s) declared that they were an editorial board member of Frontiers, at the time of submission. This had no impact on the peer review process and the final decision.
Figures
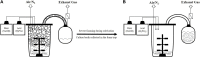
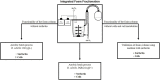
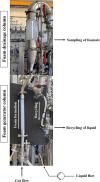
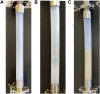

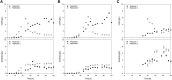
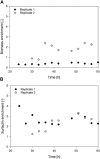
Similar articles
-
Control of agitation and aeration rates in the production of surfactin in foam overflowing fed-batch culture with industrial fermentation.Rev Argent Microbiol. 2015 Oct-Dec;47(4):344-9. doi: 10.1016/j.ram.2015.09.003. Epub 2015 Dec 4. Rev Argent Microbiol. 2015. PMID: 26655454
-
The application of foaming for the recovery of Surfactin from B. subtilis ATCC 21332 cultures.Enzyme Microb Technol. 2001 Mar 8;28(4-5):346-354. doi: 10.1016/s0141-0229(00)00327-6. Enzyme Microb Technol. 2001. PMID: 11240190
-
Integrated foam fractionation for heterologous rhamnolipid production with recombinant Pseudomonas putida in a bioreactor.AMB Express. 2016 Mar;6(1):11. doi: 10.1186/s13568-016-0183-2. Epub 2016 Feb 9. AMB Express. 2016. PMID: 26860613 Free PMC article.
-
Foam fractionation methods in aerobic fermentation processes.Biotechnol Bioeng. 2022 Jul;119(7):1697-1711. doi: 10.1002/bit.28102. Epub 2022 Apr 22. Biotechnol Bioeng. 2022. PMID: 35394649 Review.
-
Bacillus licheniformis: The unexplored alternative for the anaerobic production of lipopeptide biosurfactants?Biotechnol Adv. 2022 Nov;60:108013. doi: 10.1016/j.biotechadv.2022.108013. Epub 2022 Jun 22. Biotechnol Adv. 2022. PMID: 35752271 Review.
References
-
- Al-Masry W. A., Ali E. M., Aqeel Y. M. (2006). Effect of antifoam agents on bubble characteristics in bubble columns based on acoustic sound measurements. Chem. Eng. Sci. 61, 3610–3622. 10.1016/j.ces.2006.01.009 - DOI
-
- Alonso S., Martin P. J. (2016). Impact of foaming on surfactin production by Bacillus subtilis: implications on the development of integrated in situ foam fractionation removal systems. Biochem. Eng. J. 110, 125–133. 10.1016/j.bej.2016.02.006 - DOI
-
- Atwa N. A., El-Shatoury E., Elazzazy A., Abouzeid M. A., El-Diwany A. (2013). Enhancement of surfactin production by Bacillus velezensis NRC-1 strain using a modified bench-top bioreactor. J. Food Agric. Environ. 11, 169–174. 10.1234/4.2013.4233 - DOI
Grants and funding
LinkOut - more resources
Full Text Sources
Research Materials